I’ve been busy recently, with finishing my doctorate and a month long trip. However, I now have a fully wireless biofeedback smartwatch prototype.
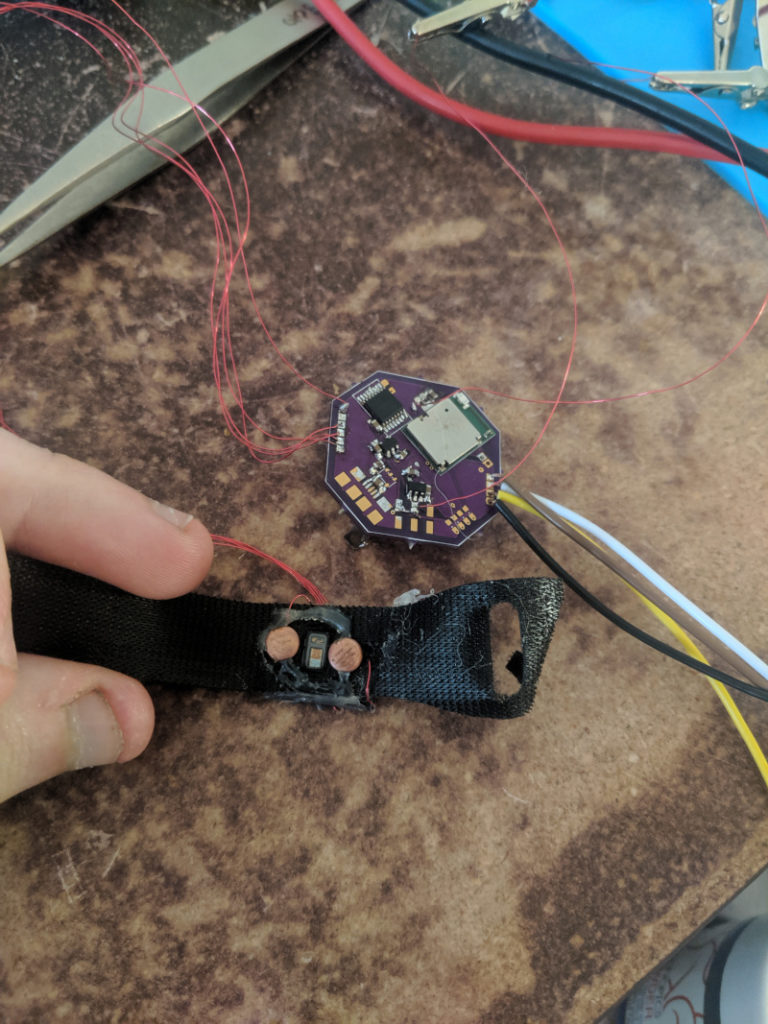
The picture is not fully assembled, but everything works other than the lack of a power switch, usb plug, and IC for charging the Li+ battery on the back. I’ve switched from using a naked nRF52810 IC to a TAIYO YUDEN module, it is more expensive, but I was having a lot of trouble getting antennas to work. The wires to the right are for programming with SWD, and the pair of magnet wires soldered to the board itself are for power so I don’t rundown the battery in testing. To the right of the module are two holes for debugging with UART; it’s been really helpful to use that and the logic analyzer to test things during development.
On the finger strap are two electrodes for the GSR voltage bridge, and the MAX30102 SPO2 sensor, which is soldered onto a PCB out of view.
I’m using the following program to activate the ADC and SPO2 sensor and broadcast data over bluetooth. I’m using the nordic UART profile, which contains two characteristics, a read and a write one. I’ve had to learn a lot more about bluetooth than I wanted to for this project.
https://github.com/garthwhelan/NRF-smartwatch/tree/master
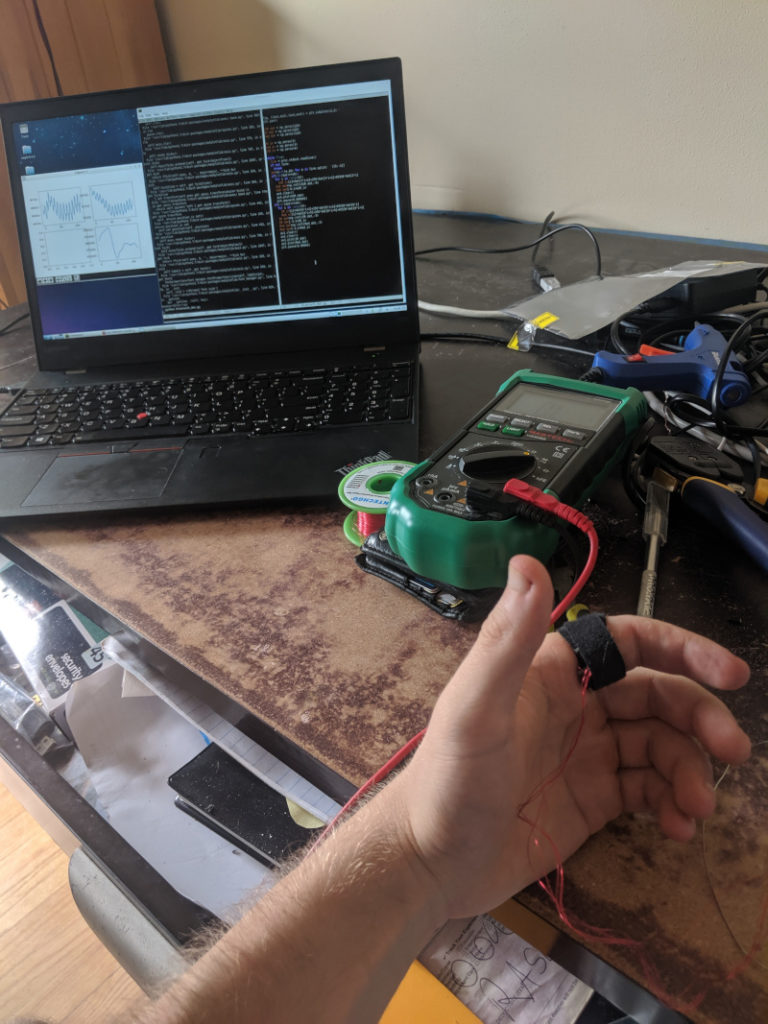
You can see in the above picture I can stream to my laptop, which live plots the data with matplotlib. I’ve had issues with plot update speeds… it sounds like pyqtgraph is a lot faster but not what I want. I’m probably going to try gnuplot if this is still an issue.
On the plotting side, it’s the same as usual, except with the source of data being:
subprocess.Popen("sudo gatttool -i hci0 -t random -b (nrf mac address) --char-write-req -a 0x10 -n 0100 --listen",shell=True,stdout=subprocess.PIPE)
Which writes 1 (0100 reverse endian) to the handle of the characteristic to enable notifications (0x10). Again, there’s a better way to do this with the actual gatt libraries.
In the end I’m pretty happy with everyting. The GSR data is a lot better since switching to a TI adc (ads1246), and the setup is not that encumbering overall. I plan on working on more data analysis for biofeedback (e.g. getting actual SPO2 values, heart rate counters,…) before doing anything with a phone app.