I made a head knife from a powder metallurgy steel (CPM 45VN) by machining the outline out of flat stock and then grinding the profiling with the help of an adjustable jig I made. For work holding, I glued the stock onto a plate and then, after drilling holes, bolted down the stock for more holding force. I was prepared for my hobby-ist grade mill to have problems but everything went beautifully.
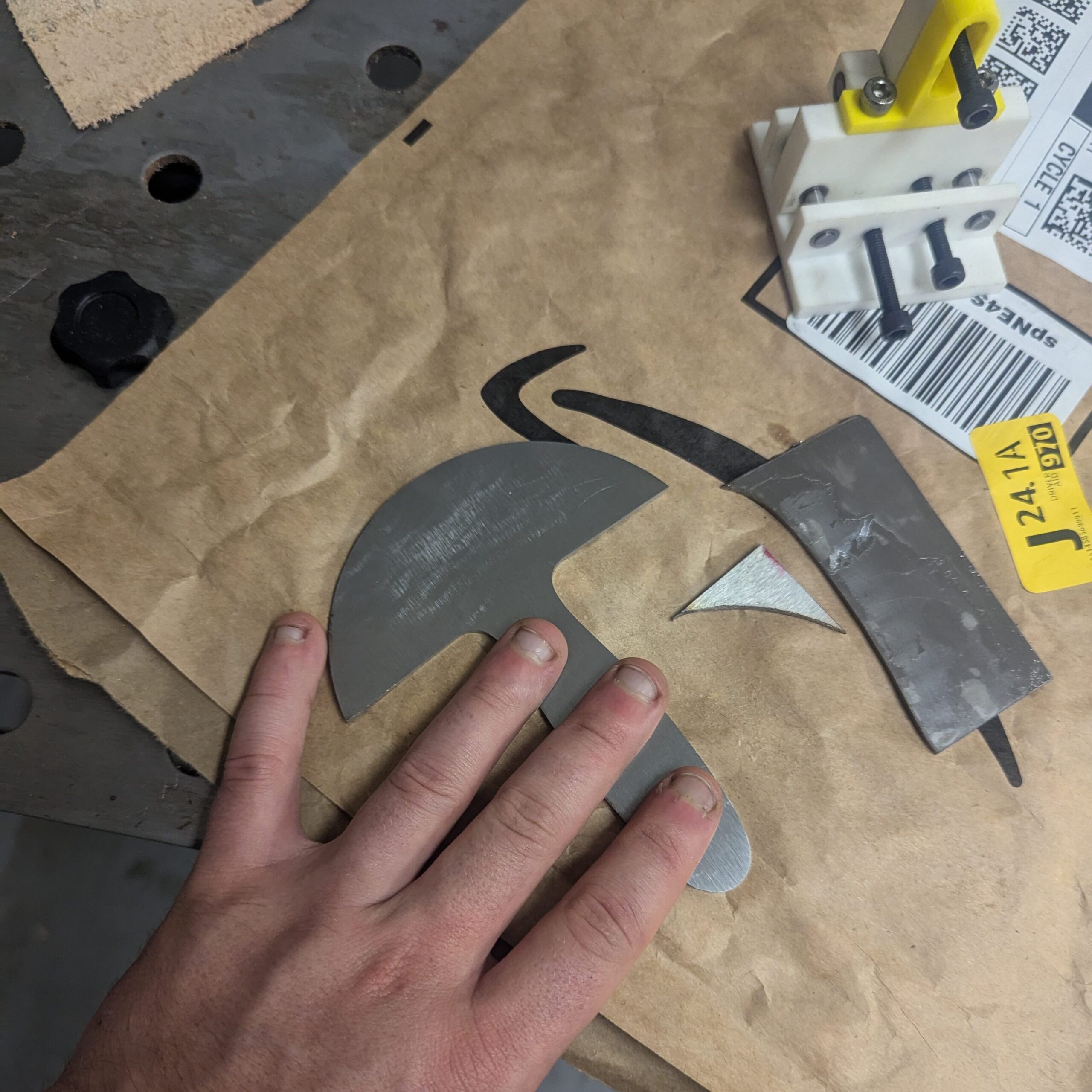
I machined the handle from Delrin. This was actually my first time working with Delrin and I was really happy with how it looks and feels. However, it’s definitely lacking in scratch resistance so the beautiful finish gets marred quickly. This was also my first project with a slitting saw, but now that I’ve used it once, I’ll probably use it often in future projects.
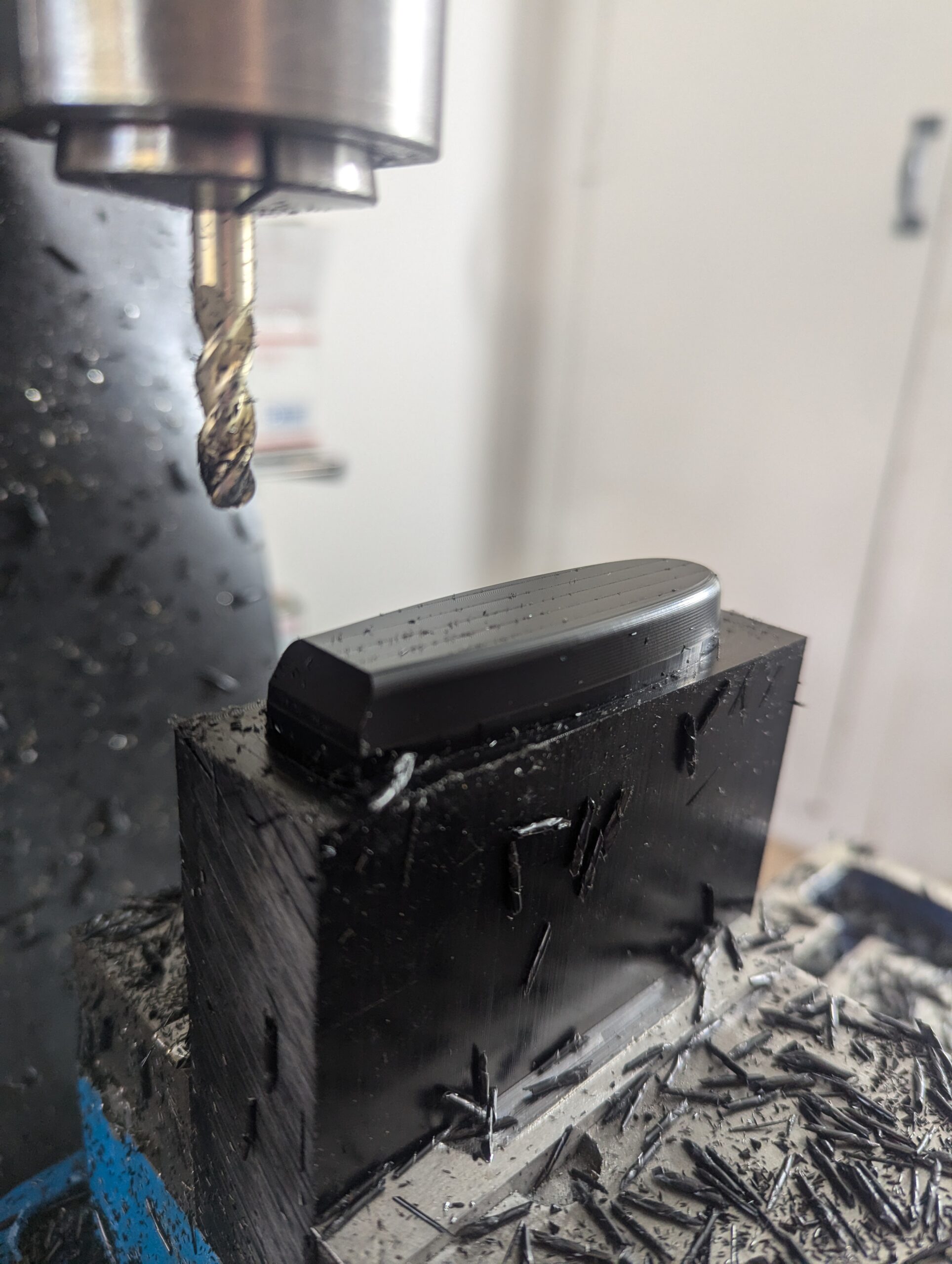
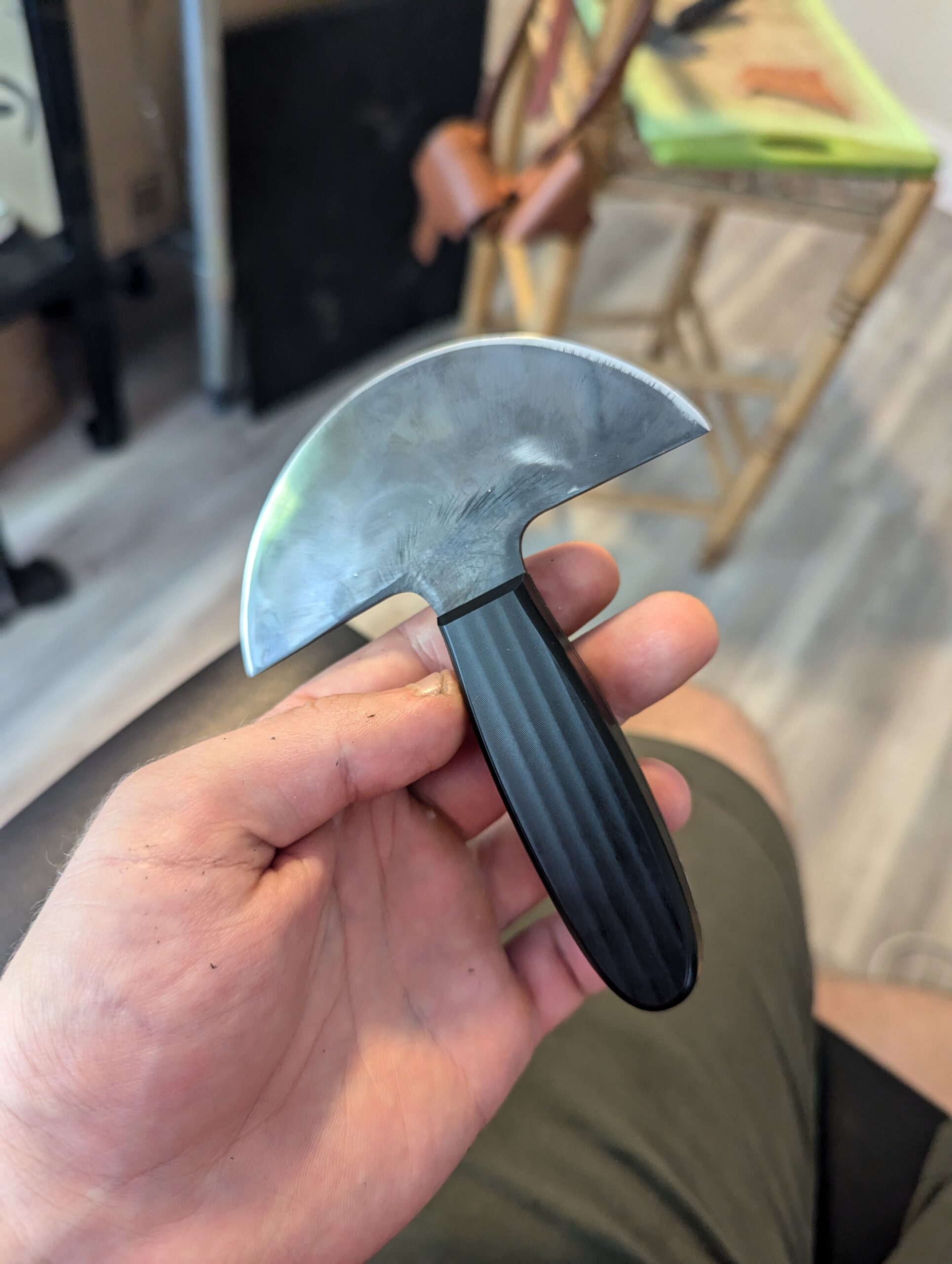